Here is a time lapse of a casing being printed on a 3d printer, this model was custom designed and was developed for Macroponics.
Uncover a realm of opportunities.
With the ability to Model and 3D print objects in Metal and plastic, I am able to craft any type of prototype quickly and reliably.
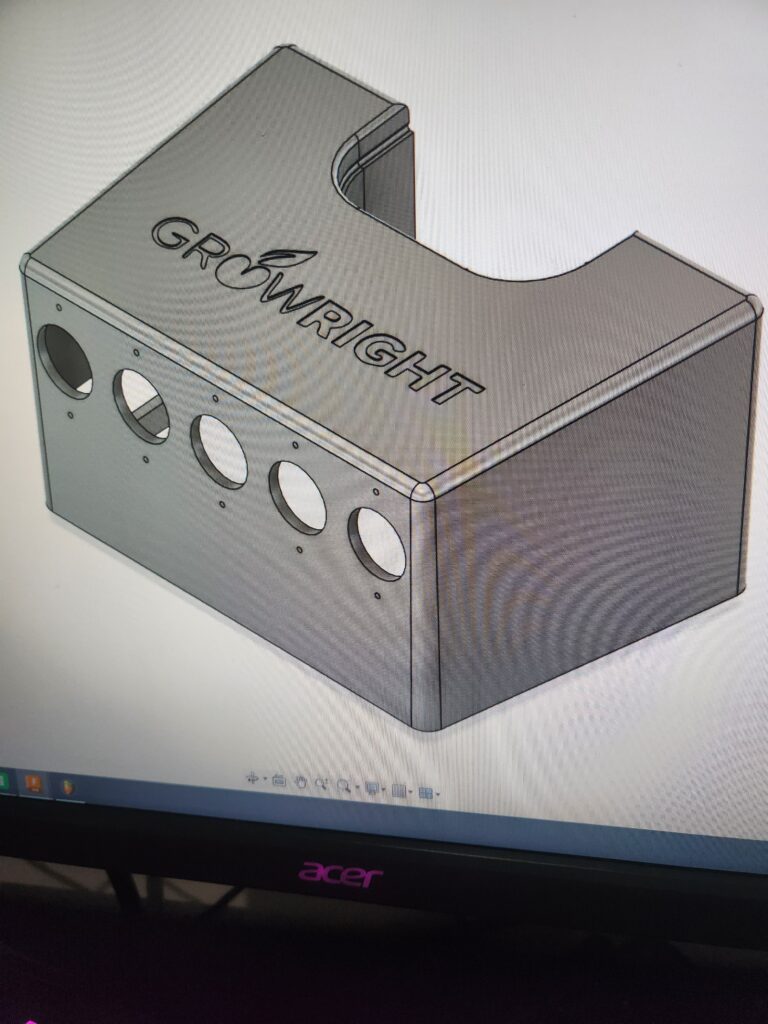
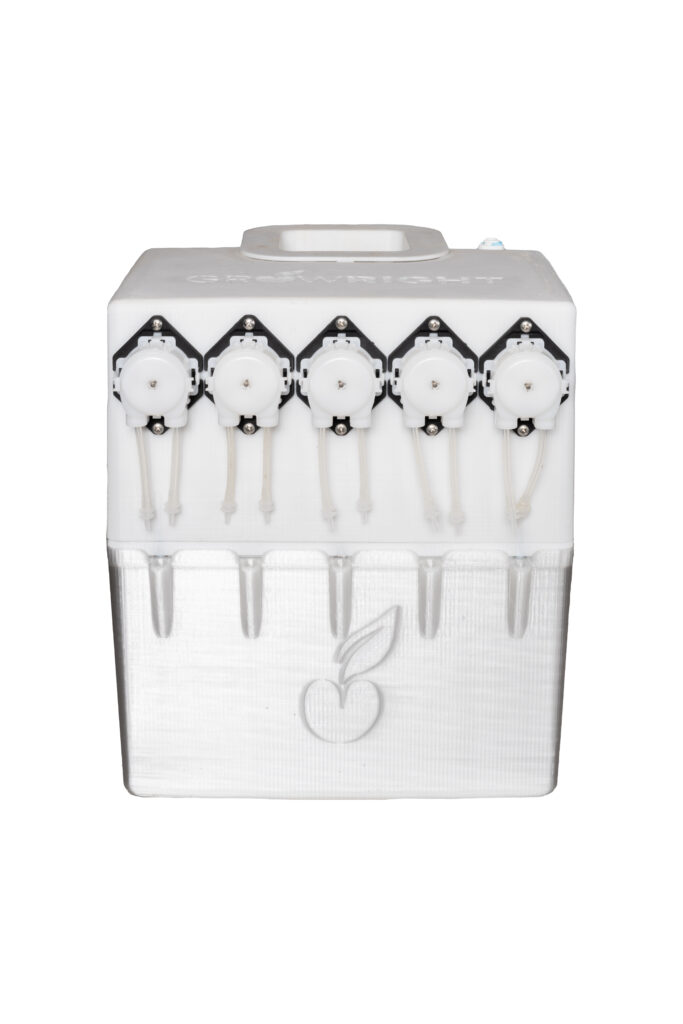
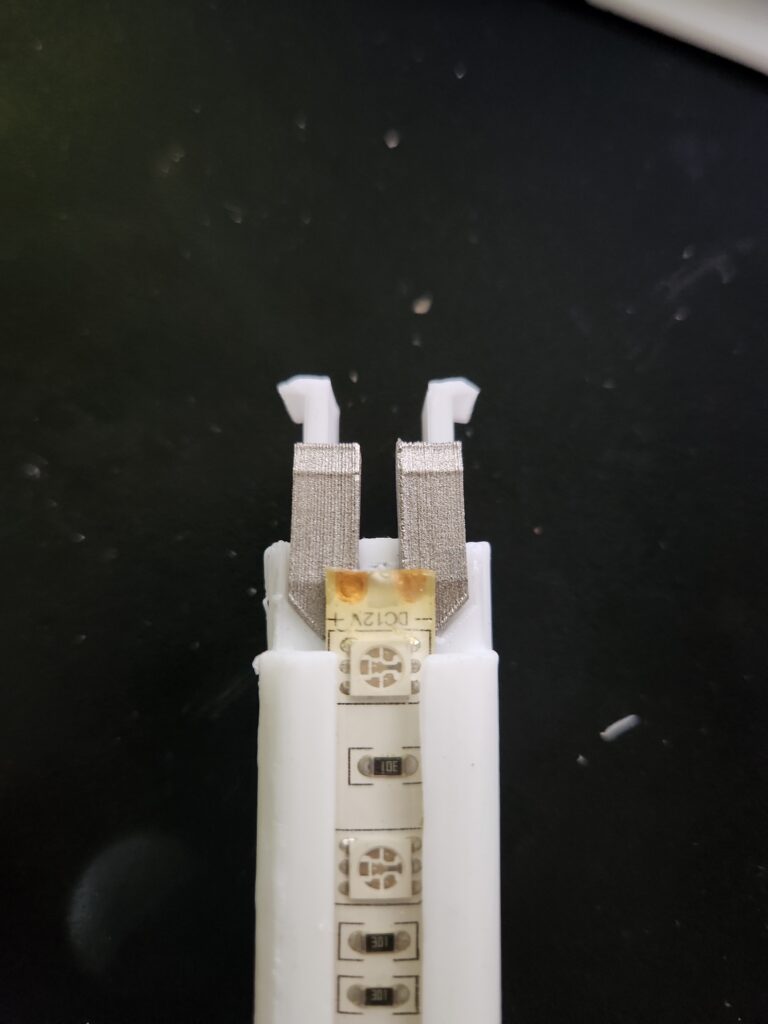
Shown below is a time lapse of the metal components that were printed for the GrowRight modular LEDs.
Re-imagine what is possible…
Do you have an idea you want to have modeled, printed and sent to you? Have questions about what is possible with 3D printing?
Tutorials can serve as valuable launching pads for anyone interested in 3D printing, offering a structured introduction to the principles of design, material science, and the intricacies of additive manufacturing. However, as many seasoned makers have discovered, true mastery of 3D printing comes from immersing yourself in hands-on experimentation and iterative learning.
This page is dedicated to the discussion of 3D printing and the vibrant community that surrounds it, a space where experienced engineers, hobbyists, and newcomers alike can share insights, innovative techniques, and practical experiences. By building a close-knit network of creators, we can collectively disseminate the most useful and up-to-date information, ensuring that everyone benefits from shared knowledge and collaborative problem solving.
Whether you’re refining your skills through meticulous prototyping or exploring new materials and cutting-edge technologies, remember that while tutorials provide the foundation, real progress is achieved through active participation and community engagement. Together, we can transform the world of 3D printing into a dynamic hub of innovation, where every challenge is an opportunity to learn and every success propels us toward even greater achievements.
The Mystical Frontier of 3D Printing: Anomalous Objects and Ethical Considerations
3D printing technology has unlocked unprecedented creative capabilities, enabling the fabrication of objects that transcend conventional boundaries. Among these are what I define as “anomalous objects”, artifacts that may carry unexpected spiritual, metaphysical, or cognitive properties. In some cases, these objects can even become what are known as info-hazards. An info-hazard is information, or, in this context, an object, that possesses the potential to cause harm simply by being known or interacted with. In the realm of 3D printing, an info-hazard might be an artifact whose anomalous properties trigger dangerous psychological effects or induce unintended physical consequences when its influence spreads.
The emergence of such artifacts forces us to confront a complex ethical landscape. While innovation is celebrated, it must be paired with the foresight to anticipate and mitigate potential risks. The creation and dissemination of anomalous objects demand a robust ethical framework, one that safeguards not only our material well-being but also our collective spiritual and cognitive health.
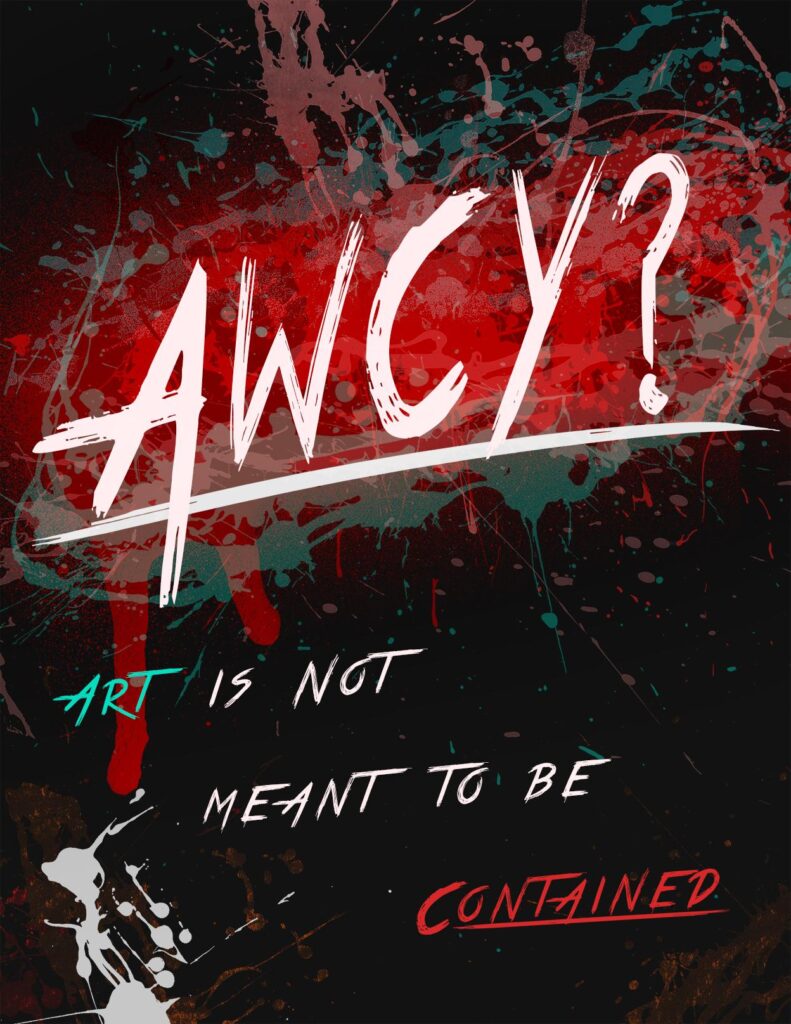
For those seeking guidance on navigating this delicate balance, I invite you to explore my guide on magick. This resource lays out an ethical framework that integrates ancient wisdom with modern technology, providing practical strategies to avoid the pitfalls associated with info-hazards. By embracing responsible practices, we can ensure that the transformative power of 3D printing remains a positive force, one that uplifts humanity and enriches our understanding of the world, rather than inadvertently unleashing chaos.